Choosing Safety Equipment That’s Ideal for Your Work Environment
If your employees work in a potentially-dangerous environment filled with heavy-duty equipment and machines, their safety should always be your number one priority. This means that you should carefully consider all your options before you buy safety equipment and personal protective apparel for your employees.
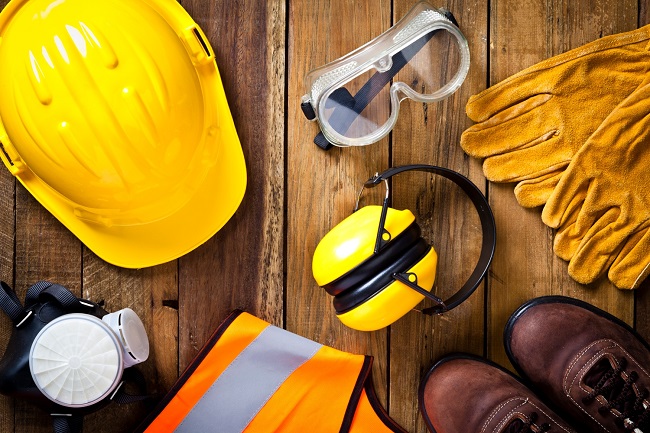
source: ambella.co.za
However, it can be difficult to know what to look for in safety equipment because not everything is created equal. You need to make sure that you buy safety equipment designed for the needs of your work environment. That being said, knowing the different types of materials used to fabricate the equipment, the various features and limitations can help you make an informed decision. Here are some factors you should consider before making your purchase.
Assess Your Work Place
Assessing the safety hazards present in your environment is the key to knowing what kind of equipment you need. Make sure you understand the real effects of each hazard. This process may need the collaboration of other people to make it easier to identify the risks and decide on the right PPE and safety equipment to get for your company staff. Consider including an independent expert who doesn’t work in the company so that he/she can make an unbiased evaluation.
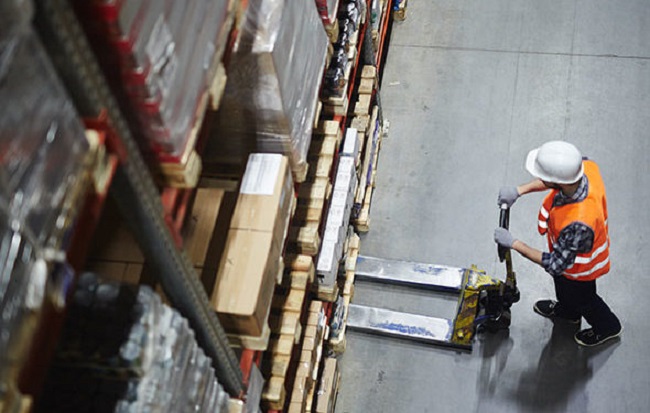
source: nowthatslogistics.com
Know The Right Gear
Before checking safety equipment online or at your local store, make sure to have an idea of what you need. Understand that the gear that an individual operating a chemical plant needs differs from that of a construction worker. After assessing the threats that your workers are faced with during their daily activities, you’ll be in a position to get them the right gear.
Some of these threats include sharp objects, impact injuries. extreme temperatures, dust, biological threats and radiation. So, when choosing the safety equipment, remember the risks you identified during the assessment phase and you will be on the right track.
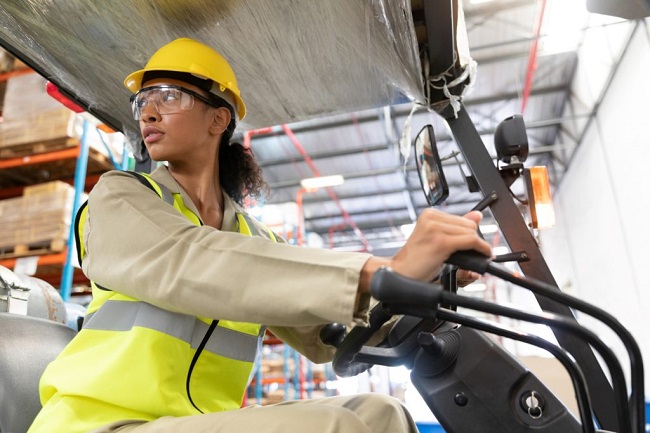
source: safesitehq.com
When it comes to choosing the right safety gear, know that apparel isn’t the only element to consider. In other words, you also need to make sure that the tools your workers use daily are safe and don’t carry the risk of injury. For instance, if the job involves cutting, then make sure to pick safety knives that provide a secure grip and stability. Safety knives are ideal for warehouse and industrial workers.
If the job is outside or involves a heavy flow of traffic, make sure you have suitable signalling in place. There’s a wide range of traffic control supplies that can reduce the risk of accidental collision, like for instance stop signs, traffic cones, traffic lights, mirrors and wheel stops.
If you’re responsible for a warehouse, make sure that the pallets are protected with rack post protectors to reduce the risk of falls and injuries. Mezzanine safety gates may be another worthwhile addition for a warehouse.
Consider Fit, Flexibility and Weight
Does the garments you are considering allow a full range of motion and allow the wearer to perform the job function without difficulty? Keep in mind that with protective apparel, there is no one-size-fits-all solution. Ask your employees to try on the garments to ensure a good fit.
Flexibility and weight are other important factors because they also affect the wearer’s range of motion and extent of job fatigue. Although lightweight, limited-use protective apparel offers great advantages over recyclable garments, lightweight fabrics must also be strong enough to withstand the rigorous of the workplace.
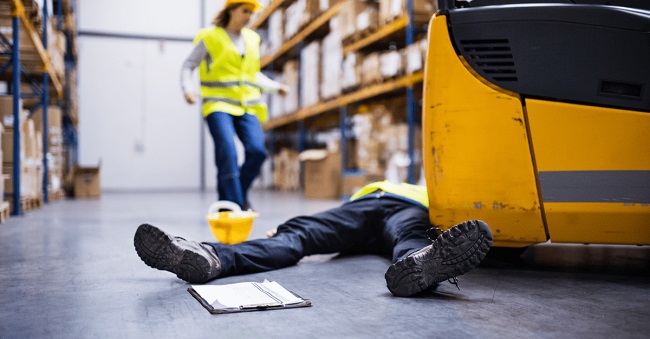
source: cyzerg.com
Weight is also an important factor to consider when buying safety equipment such as mezzanine gates. Make sure that they have the right weight capacity to support the weight of the workers as well as any other load that they may need to carry.
Ensuring that the protective apparel and safety equipment is designed and made from the right materials may be the most important of all wearability issues. By providing your employees with apparel that offers protection and good-quality features, you will be encouraging them to make use of their gear and achieve a higher level of personal protection.
Choose Quality and Durability Over Price
The material and design of the safety equipment are what will determine it’s durability. For example, if you choose a helmet that has been made from the cheapest plastic, it will not serve you or your employees for more than a couple of weeks. Choose gear that will serve your employees for a long time.
Some of this equipment may come with information tags detailing how long they can last. Note that the product’s durability will be affected by the environment where it’s used, so check the warranty that the manufacturer offers to determine the issues it covers. If you’re working outdoors, it’s better to choose stainless steel safety equipment that won’t easily rust.
When it comes to quality, never make compromises for a lower price tag. Go for the highest quality you can afford and choose products that have met the specified standards. For example, if you get your workers footwear made from cheap material, this footwear might not prevent the risk of static discharge, which can cause serious injuries. So, make sure the finest materials and quality build have been used by the manufacturer in the production of the safety equipment.
Provide Proper Training: Wear, Care and Disposal
It’s your obligation to provide your workers with proper training on how to put the equipment on, take it off, use and adjust it. This will be a great time to confirm the sizing because relying on the sizing charts is not always enough. You don’t want for size to be a problem, too large shoes or pants may lead to tripping and may present movement hazards like snags, tears or rips.
Make sure your workers understand how the equipment can impact the type of job they do. You must ensure that they know how to wear and use the safety equipment by simulating the working environment and activities they usually perform.
Establish Checks and Controls
Keeping track of the equipment you provided and how often replacements for it is requested by personnel will help you determine whether items are not being used properly or are being stolen. Safety equipment that worn quickly can also be a sign that the items used are not suited for the environment or that work processes need to be changed.