Hydraulic Press Brake Machine: The Ideal Investment for Metal Fabrication Businesses
Posted in Industrial Equipment By Ben Eliot On May 20, 2025Hydraulic press brakes are mainstays of today’s modern metalworking and fabrication industries. From the heavyweight structural panel stampings used in the oil and gas industries, to the high-volume/high-precision blanks that are pressed out by the hundreds for automobiles and appliances, when it comes to precise metal shaping and forming, hydraulic presses are impossible to beat.
Experienced fabricators understand, however, that while the powering options for presses may vary, the biggest difference between modern hydraulic presses and their mechanical-, and pneumatic-powered counterparts isn’t as much about how they’re powered or their bed sizes as it is about their level of automated control.
Automatic controls allow operators to take the fullest advantage of a hydraulic press’s size, power, and potential throughput. These are all factors leading to increases in precision and efficiency, therefore making automated hydraulic presses a vastly better investment over the long run.
Automated Controls Bring Out the Best in Hydraulic Press Brakes
Let’s face it: with bending lengths up 6000 mm and bending capacities up to 400 tonnes, when compared with other types of industrial presses, a modern hydraulic press brake machine is a force to recon with. Its consistent compressive force easily exceeds that of the highest performing mechanical and pneumatic presses, and it’s more than capable of maintaining the precision of standard servo-, and other hybrid-type presses. With NC (Numeric Controlled) or CNC (Computer Numeric Controlled) automation, however, hydraulic presses are able to perform their core fabrication processes faster, more accurately and more predictably, including:
- Bending and forming metal sheets, coils, and blanks;
- Cutting and punching all types of materials;
- Forging, moulding, and stamping individual components;
- Clinching and joining tight-fitting parts and panels; and,
- Compacting material for other manufacturing processes.
Invariably, with automated controls, fabricators don’t have to be as reliant on, or limited by operator proficiency as they would with a press brake that requires extensive manual control and oversight. And the result is, businesses are able to pare back on their costs while simultaneously increasing their output.
Versatile NC Controls Increase Hydraulic Press Brake Efficiency
Although NC controlled hydraulic press brake machines are far from optimal for either large or exceptionally small scale production runs, the advantages that they have over manually controlled presses are still nothing short of business-changing. With capacities up to 175 tonnes and throughputs up to 8 strokes per minute (SPM), once they’ve been programmed, 2 axis NC controlled press brakes require little more than minor adjustments and feeding by the operator to produce their full benefits, which include:
- Increased efficiency. Efficiency is crucial for every business’s sustainability, and NC controlled hydraulic press brakes can be set up almost instantly with virtually no loss of productivity due to down time, and offering greater flexibility when it comes to production scheduling.
- Consistent metal processing. With its electronically controllable programming and accurate repeat action, an NC controlled hydraulic press brake is perfect for moderate-sized runs of error-free output, while requiring only minimal human intervention.
- Versatile, low effort functionality. NC controlled hydraulic presses are able to perform all types of blanking, bending and punching tasks, and can work with a full range of metals such as steel, brass or aluminium.
Ideally, with the ability to work with materials up to several centimetres thick, an NC controlled hydraulic press brake machine is sufficient for all but the most complex punching and fabricating jobs. However, when businesses need the multi-stage accuracy, capacity and flexibility to change the design of product outputs instantaneously, only CNC controlled hydraulic press brakes can fit the bill.
CNC Controls Are the Key to Reining In Hydraulic Press Brake Costs
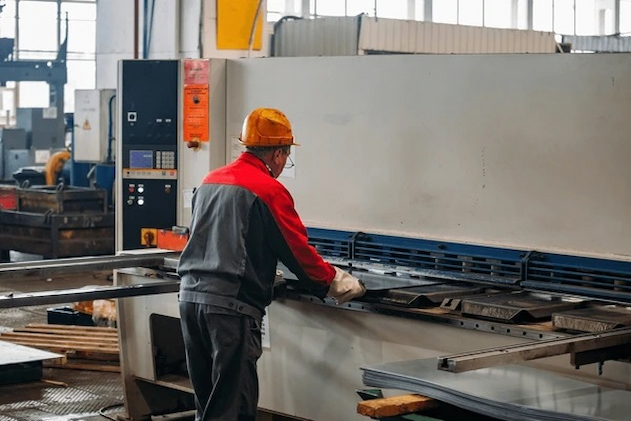
Unlike 2 axis NC controlled presses that are engineered strictly for simple setup and production tasks, semi- and fully-automated CNC controlled hydraulic press brakes are built for complex 4-8 axis fabrication activities. Their ability to store and recall multiple programming setups is central to their advanced programmability. When combined with standard >250 tonne press capacities and >4200 mm bending lengths, it’s the perfect solution for intricate and irregularly shaped panels for oversized metalworks.
That makes them ideal for the production of HVAC system components, distribution cabinets and panels, and aerospace airframe components without the need for multiple passes. CNC controlled pressbrakes are designed to build on the same key qualities of increased efficiency, consistency and versatility that NC controlled machines have over manual presses. Their most impressive advantages over NC presses come from factors away from the finished product though, and they include:
- Reductions in material waste. Materials can account for 40 – 50% or more of the cost of most major end items. The precision of CNC controlled press brake machines for sale allows fabricators to maximise their raw material stock usage, while simultaneously reducing waste falloff and the need for even costlier rework.
- Increased operator safety. Press brakes, like all heavy-duty plant equipment are dangerous. Unlike presses that require extensive manual setup and feeding though, CNC controlled press brakes require almost no human intervention, making them both safer and less prone to incorrect operation.
- Improved cost oversight. Even under the best of conditions, cost is a constant concern in manufacturing. However, when it comes to ordering raw materials and calculating manpower requirements, CNC controlled presses give businesses the unparalleled ability to automatically and predictably regulate every aspect of their fabrication process costs.
Make no mistake: while CNC controlled hydraulic press brakes represent a significantly steeper initial investment when compared with NC controlled units, their accuracy, efficiency, and cost effectiveness ultimately gives them a long term advantage. They also make it possible for fabricators to take on a wider range of projects, thereby also allowing them to add directly to their bottom line.
The Final Word
At the end of the day, businesses that depend on heavy metal fabrication can’t afford to find themselves burdened behind inefficient machinery. That includes press brakes, where continuing to operate under-powered and under-performing machines can cost a business more than taking a fresh look at ones that put the strength of hydraulic compression and automated controls to full use. A modern NC or CNC controlled hydraulic press machine has everything a metal fabricator needs to give their business the production and cost edge. It’s an investment in productivity, efficiency and safety that every fabricator needs to consider.
About Author
ben